精密制造双引擎:CNC 加工与钣金加工的协同创新解析
发布时间:
2025-05-09
CNC加工与钣金加工是精密制造的双核心技术,各有优势。CNC加工以减法制造为核心,多维度切削能力强大;而钣金加工则以加法制造,冷加工工艺实现轻量化结构件。材料选择与行业应用深度适配,复合材料的兴起推动工艺融合。
在现代工业体系中,CNC加工与钣金加工构成了精密制造的双核心技术。CNC加工通过数字化控制实现复杂零件的高精度切削,而钣金加工则通过冷成型技术将金属薄板转化为结构件。两者在工艺原理、材料适配性和应用场景上形成互补,共同推动机械制造、汽车、电子等行业的技术升级。椿田机械凭借20年技术积淀,在泰国与马来西亚分别布局钣金与CNC加工基地,构建覆盖全球的高效制造网络,为客户提供从设计到量产的全链条解决方案。
核心工艺对比:从切削成型到冷加工的技术分野
CNC加工以减法制造为核心,通过数控系统控制刀具对坯料进行铣削、车削等切削操作,可实现微米级精度。其优势在于复杂曲面加工能力,例如航空航天领域的叶轮部件需通过五轴联动CNC机床完成多维度切削。而钣金加工属于加法制造,通过激光切割、折弯、焊接等冷加工工艺,将金属板材转化为薄壁结构件,典型应用如新能源汽车电池壳体的一体化成型。两者在工艺逻辑上形成互补:CNC加工擅长单件高精度定制,钣金加工则适合批量生产轻量化结构件。
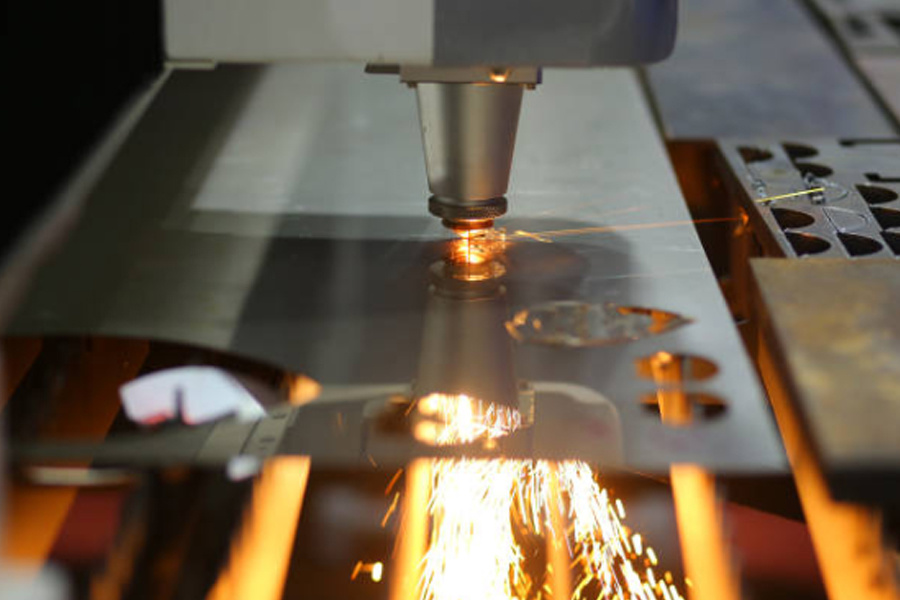
材料选择与行业应用的深度适配
CNC加工对材料硬度和韧性要求较高,常用材料包括铝合金(如 7075-T6)、钛合金(如 TC4)及高强度钢(如 H13 模具钢)。以医疗设备为例,CNC加工的不锈钢关节部件需满足 ISO 13485 标准的生物相容性要求。钣金加工则更侧重材料的成型性能,冷轧板(SPCC)因易折弯成为家电外壳首选,镀锌板(SECC)凭借耐蚀性广泛应用于汽车底盘。值得关注的是,复合材料(如碳纤维增强塑料)的兴起正推动两种工艺的融合,例如:CNC加工完成复合材料模具后,再通过钣金工艺实现轻量化结构件的批量生产。
技术创新与行业趋势的深度融合
智能化升级:CNC加工引入AI算法优化刀具路径,通过实时监测系统将加工误差降低至 ±5μm 以内;钣金加工则借助工业机器人实现折弯角度的自动校准,良品率提升至98%以上。椿田机械在马来西亚工厂部署的 MES 系统,可实现CNC加工参数的云端实时调整,订单响应速度提升40%。
绿色制造转型:CNC加工通过干式切削技术减少切削液使用量,而钣金加工采用激光切割替代传统冲压,材料利用率从65%提升至85%。泰国工厂引入的光伏供电系统,使钣金加工的单位能耗降低 20%,符合欧盟 RoHS 环保指令要求。
工艺协同创新:在5G通信设备制造中,CNC加工完成散热模块的精密腔体后,通过钣金工艺实现外壳的无缝拼接,最终产品散热效率较传统方案提升30%。这种“精密切削+薄壁成型”的组合模式,正成为高端制造领域的主流技术路线。
CNC 加工与钣金加工的技术演进,本质上是数字化控制与材料科学深度融合的产物。椿田机械通过泰国与马来西亚双基地布局,实现了 “东南亚产能 + 全球服务” 的战略协同,可快速响应客户从原型开发到规模化生产的全周期需求。未来,随着工业互联网与增材制造技术的渗透,这两种工艺将进一步向“高精度、低能耗、全流程数字化”方向发展,成为驱动智能制造升级的核心引擎。
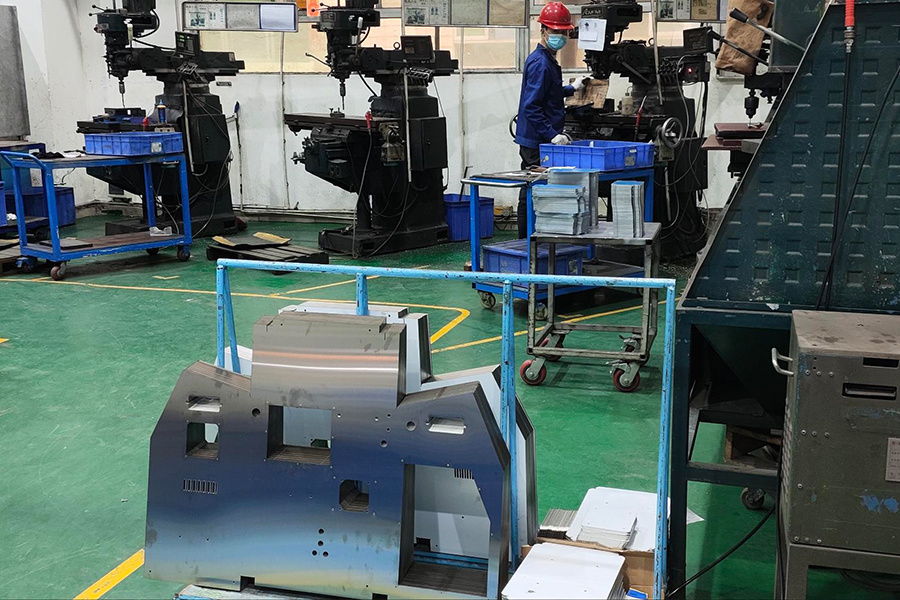
常见问题解答
Q1:如何选择 CNC 加工与钣金加工?
A1:若零件需复杂内部结构(如液压阀体)或高精度表面(Ra≤0.8μm),优先选择 CNC 加工;若为薄壁壳体类零件(厚度≤3mm)且需批量生产,钣金加工更具成本优势。两者亦可协同使用,例如 CNC 加工关键连接部件,钣金工艺完成外围框架制造。
Q2:材料特性对加工工艺的影响?
A2:高强度铝合金(如 6061-T6)适合 CNC 铣削,但需注意切削热导致的变形;不锈钢(SUS304)在钣金折弯时易产生回弹,需通过预弯补偿算法优化。对于钛合金(Ti-6Al-4V),CNC 加工需采用金刚石涂层刀具,并配合高压冷却系统。
Q3:表面处理工艺如何选择?
A3:CNC 加工零件多采用阳极氧化(如硬质阳极氧化膜厚≥25μm)或 PVD 涂层提升耐磨性;钣金件则常用粉末喷涂(膜厚 60-80μm)或镀锌(镀层厚度 8-12μm)增强耐蚀性。椿田机械提供从发黑处理到电泳涂装的全系列表面解决方案,满足不同应用场景需求。